Gluing in the Soundboard
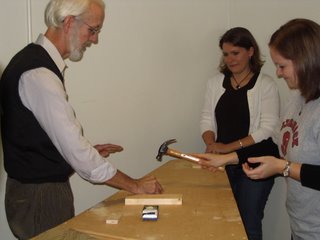
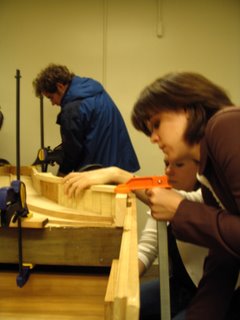
This view shows the keyboard end.

With the keyboards in place, we can start to imagine how it will look completed.

Grad students at Duke University convene to build an 18th century French double manual Hubbard harpsichord kit.
This view shows the underside of the soundboard with ribs, cutoff bar, and rose all in place. The white muslin glued to the ends of the ribs and around the rose helps to strengthen these areas.
Paul is gluing on the 4' hitchpin rail. This piece will hold the hitchpins for the 4' set of strings. The soundboard is very thin and it would not be able to hold them securely without this piece. Jessica and Paul clean up the excess glue after clamping. Note the long clamping bars which span our workbench.
Once all the glue has dried on all the parts attached to the soundboard, the top is cleaned up so no glue or other marks show.
The soundboard measures exactly 36 1/4 inches--the same size as when we fitted it to the case some weeks ago. That means that the humidity is just right for installing it into the case.
The bridge for the 8 foot choir of strings is being marked for installation. The procedure is similar to how the nuts were attached to the wrestplank.
Beneath the bridge (here shown upsidedown) are the plans which show the exact location for the bridge on the soundboard.